IMQCAM research impact
Additive manufacturing technology has offered incredible benefits in wide-spread applications, design flexibility, affordability, schedule, performance, sustainability, and production on demand. However, certification is the greatest challenge to its adoption due to its complexity, unknowns, and delays, which can significantly negate its benefits. Certification of remotely produced products is also an unresolved technology gap.
Current approaches for certification rely heavily on trial and error, where the outcomes from numerous combinations of parameters are evaluated experimentally. Iteration may occur on a particular part built numerous times to “dial in” the recipe, and endless variations arise due to the sensitive nature of the metallurgical process and individual aspects of AM machines.
The mission of the IMQCAM is to develop an end-to-end model or digital twin of the LPBF process, connecting feedstock, 3D printing conditions, and post-print microstructural state to part response, location-specific properties, and fatigue life, which is crucial to the aerospace community.
As motivation for the IMQCAM, Mallory James at NASA-Marshall says: “Advancement of computational tools for certification enables a transition from Design-Build-Test paradigm to Design-Model-Build.”
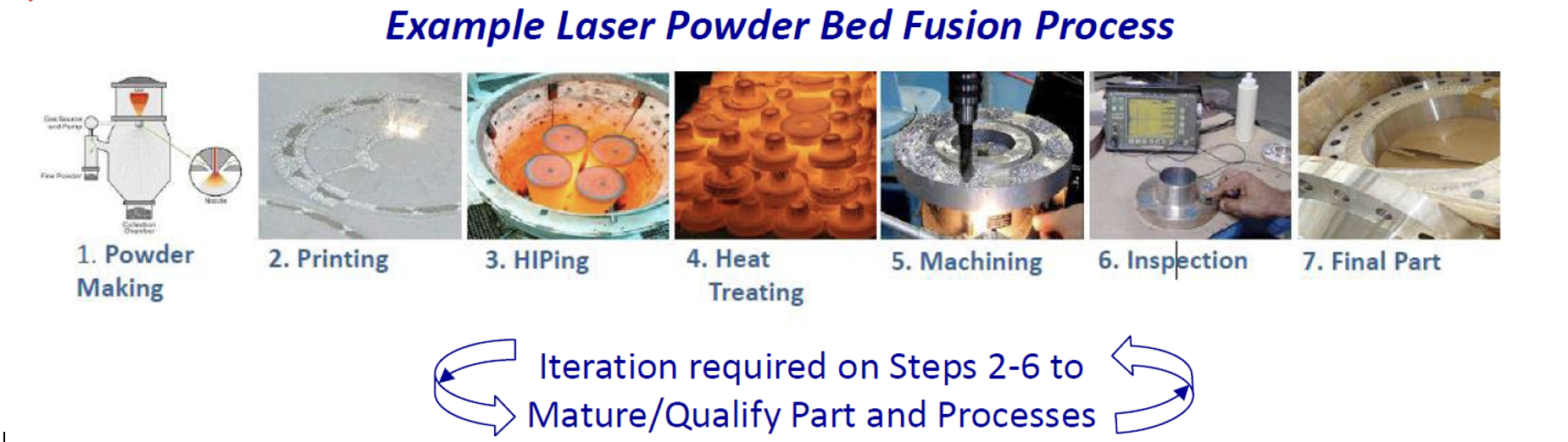